সাম্প্রতিক বছরগুলিতে, নতুন শক্তি শিল্পের দ্রুত বিকাশের জন্য ধন্যবাদ, লেজার ঢালাই দ্রুত এবং স্থিতিশীল সুবিধার কারণে সম্পূর্ণ নতুন শক্তি শিল্পে দ্রুত প্রবেশ করেছে। তাদের মধ্যে, লেজার ঢালাই সরঞ্জাম সমগ্র নতুন শক্তি শিল্পে অ্যাপ্লিকেশনের সর্বোচ্চ অনুপাতের জন্য অ্যাকাউন্ট।
লেজার ঢালাইদ্রুত গতি, বৃহৎ গভীরতা এবং ছোট বিকৃতির কারণে দ্রুত জীবনের সকল ক্ষেত্রে প্রথম পছন্দ হয়ে উঠেছে। স্পট ওয়েল্ড থেকে বাট ওয়েল্ড, বিল্ড আপ এবং সিল ওয়েল্ডস,লেজার ঢালাইঅতুলনীয় নির্ভুলতা এবং নিয়ন্ত্রণ প্রদান করে। এটি সামরিক শিল্প, চিকিৎসা সেবা, মহাকাশ, 3C অটো যন্ত্রাংশ, যান্ত্রিক শীট ধাতু, নতুন শক্তি এবং অন্যান্য শিল্প সহ শিল্প উত্পাদন এবং উত্পাদনে একটি গুরুত্বপূর্ণ ভূমিকা পালন করে।
অন্যান্য ঢালাই প্রযুক্তির সাথে তুলনা করে, লেজার ঢালাই এর অনন্য সুবিধা এবং অসুবিধা রয়েছে।
সুবিধা:
1. দ্রুত গতি, বড় গভীরতা এবং ছোট বিকৃতি।
2. ঢালাই স্বাভাবিক তাপমাত্রায় বা বিশেষ অবস্থার অধীনে সঞ্চালিত হতে পারে, এবং ঢালাই সরঞ্জাম সহজ. উদাহরণস্বরূপ, একটি লেজার রশ্মি একটি ইলেক্ট্রোম্যাগনেটিক ক্ষেত্রে প্রবাহিত হয় না। লেজারগুলি ভ্যাকুয়াম, বায়ু বা নির্দিষ্ট গ্যাস পরিবেশে ঢালাই করতে পারে এবং কাচের মধ্য দিয়ে বা লেজার রশ্মিতে স্বচ্ছ সামগ্রী ঢালাই করতে পারে।
3. এটি টাইটানিয়াম এবং কোয়ার্টজের মতো অবাধ্য উপকরণগুলিকে ঝালাই করতে পারে এবং ভাল ফলাফলের সাথে ভিন্ন উপকরণগুলিকেও ঝালাই করতে পারে।
4. লেজার ফোকাস করার পরে, পাওয়ার ঘনত্ব বেশি। আকৃতির অনুপাত 5:1 পৌঁছতে পারে এবং উচ্চ-শক্তির ডিভাইসগুলি ঢালাই করার সময় 10:1 পর্যন্ত পৌঁছতে পারে৷
5. মাইক্রো ঢালাই সঞ্চালিত করা যেতে পারে. লেজার রশ্মি ফোকাস করার পরে, একটি ছোট স্পট পাওয়া যেতে পারে এবং সঠিকভাবে অবস্থান করা যেতে পারে। স্বয়ংক্রিয় ভর উত্পাদন অর্জনের জন্য এটি মাইক্রো এবং ছোট ওয়ার্কপিসগুলির সমাবেশ এবং ঢালাইতে প্রয়োগ করা যেতে পারে।
6. এটি হার্ড-টু-নাগালের এলাকায় ঢালাই করতে পারে এবং অ-যোগাযোগ দূর-দূরত্বের ঢালাই করতে পারে, মহান নমনীয়তার সাথে। বিশেষ করে সাম্প্রতিক বছরগুলিতে, YAG লেজার প্রক্রিয়াকরণ প্রযুক্তি অপটিক্যাল ফাইবার ট্রান্সমিশন প্রযুক্তি গ্রহণ করেছে, যা লেজার ওয়েল্ডিং প্রযুক্তিকে আরও ব্যাপকভাবে প্রচার এবং প্রয়োগ করতে সক্ষম করেছে।
7. লেজার রশ্মিটি সময় এবং স্থানের মধ্যে বিভক্ত করা সহজ, এবং একাধিক বিম একই সাথে একাধিক স্থানে প্রক্রিয়া করা যেতে পারে, আরও সুনির্দিষ্ট ঢালাইয়ের জন্য শর্ত প্রদান করে।
ত্রুটি:
1. ওয়ার্কপিসের সমাবেশ নির্ভুলতা উচ্চ হওয়া প্রয়োজন, এবং ওয়ার্কপিসের উপর মরীচির অবস্থান উল্লেখযোগ্যভাবে বিচ্যুত হতে পারে না। এর কারণ হল ফোকাস করার পর লেজারের স্পট সাইজ ছোট এবং ওয়েল্ড সীম সংকীর্ণ, যার ফলে ফিলার মেটাল মেটেরিয়াল যোগ করা কঠিন হয়ে পড়ে। যদি ওয়ার্কপিসের সমাবেশ নির্ভুলতা বা মরীচির অবস্থান নির্ভুলতা প্রয়োজনীয়তা পূরণ না করে, ঢালাই ত্রুটি ঘটতে পারে।
2. লেজার এবং সম্পর্কিত সিস্টেমের খরচ বেশি, এবং এককালীন বিনিয়োগ বড়।
সাধারণ লেজার ঢালাই ত্রুটিলিথিয়াম ব্যাটারি উত্পাদন
1. ঢালাই porosity
মধ্যে সাধারণ ত্রুটিলেজার ঢালাইছিদ্র হয় ঢালাই গলিত পুল গভীর এবং সরু। লেজার ঢালাই প্রক্রিয়া চলাকালীন, নাইট্রোজেন বাইরে থেকে গলিত পুল আক্রমণ করে। ধাতুর শীতলকরণ এবং দৃঢ়করণ প্রক্রিয়ার সময়, তাপমাত্রা হ্রাসের সাথে নাইট্রোজেনের দ্রবণীয়তা হ্রাস পায়। যখন গলিত পুল ধাতুটি স্ফটিক হতে শুরু করতে শীতল হয়, তখন দ্রবণীয়তা তীব্রভাবে এবং হঠাৎ করে কমে যাবে। এই সময়ে, বুদবুদ গঠনের জন্য প্রচুর পরিমাণে গ্যাস প্রবাহিত হবে। বুদবুদের ভাসমান গতি ধাতব স্ফটিকের গতির চেয়ে কম হলে ছিদ্র তৈরি হবে।
লিথিয়াম ব্যাটারি শিল্পের অ্যাপ্লিকেশনগুলিতে, আমরা প্রায়শই দেখতে পাই যে পজিটিভ ইলেক্ট্রোডের ঢালাইয়ের সময় ছিদ্রগুলি বিশেষভাবে ঘটতে পারে, তবে নেতিবাচক ইলেক্ট্রোডের ঢালাইয়ের সময় খুব কমই ঘটে। কারণ পজিটিভ ইলেক্ট্রোড অ্যালুমিনিয়াম দিয়ে এবং নেতিবাচক ইলেক্ট্রোড তামা দিয়ে তৈরি। ঢালাইয়ের সময়, অভ্যন্তরীণ গ্যাস সম্পূর্ণভাবে উপচে পড়ার আগে পৃষ্ঠের তরল অ্যালুমিনিয়াম ঘনীভূত হয়, যা গ্যাসকে উপচে পড়া এবং বড় এবং ছোট গর্ত তৈরি করতে বাধা দেয়। ছোট স্টোমাটা।
উপরে উল্লিখিত ছিদ্রের কারণগুলি ছাড়াও, ছিদ্রগুলির মধ্যে বাইরের বাতাস, আর্দ্রতা, পৃষ্ঠের তেল ইত্যাদি অন্তর্ভুক্ত রয়েছে। উপরন্তু, নাইট্রোজেন প্রবাহিত হওয়ার দিক এবং কোণও ছিদ্র গঠনকে প্রভাবিত করবে।
কিভাবে ঢালাই ছিদ্র ঘটনা কমাতে?
প্রথম, আগেঢালাই, আগত উপকরণের পৃষ্ঠের তেলের দাগ এবং অমেধ্য সময়মতো পরিষ্কার করা প্রয়োজন; লিথিয়াম ব্যাটারি উত্পাদন, ইনকামিং উপাদান পরিদর্শন একটি অপরিহার্য প্রক্রিয়া.
দ্বিতীয়ত, ঢালাইয়ের গতি, শক্তি, অবস্থান, ইত্যাদির মতো কারণগুলির সাথে শিল্ডিং গ্যাসের প্রবাহ সামঞ্জস্য করা উচিত এবং খুব বড় বা খুব ছোটও হওয়া উচিত নয়। প্রতিরক্ষামূলক ক্লোকের চাপ লেজারের শক্তি এবং ফোকাস অবস্থানের মতো কারণগুলির সাথে সামঞ্জস্য করা উচিত এবং খুব বেশি বা খুব কম হওয়া উচিত নয়। প্রতিরক্ষামূলক ক্লোকের অগ্রভাগের আকৃতিটি ঢালাইয়ের আকৃতি, দিক এবং অন্যান্য কারণ অনুসারে সামঞ্জস্য করা উচিত যাতে প্রতিরক্ষামূলক পোশাকটি ঢালাইয়ের জায়গাটিকে সমানভাবে আবৃত করতে পারে।
তৃতীয়ত, ওয়ার্কশপে বাতাসে তাপমাত্রা, আর্দ্রতা এবং ধুলো নিয়ন্ত্রণ করুন। পরিবেষ্টিত তাপমাত্রা এবং আর্দ্রতা সাবস্ট্রেটের পৃষ্ঠের আর্দ্রতা এবং প্রতিরক্ষামূলক গ্যাসকে প্রভাবিত করবে, যা ফলত গলিত পুলে জলীয় বাষ্পের উত্পাদন এবং অব্যাহতিকে প্রভাবিত করবে। যদি পরিবেষ্টিত তাপমাত্রা এবং আর্দ্রতা খুব বেশি হয়, তাহলে সাবস্ট্রেটের পৃষ্ঠে অত্যধিক আর্দ্রতা এবং প্রতিরক্ষামূলক গ্যাস থাকবে, প্রচুর পরিমাণে জলীয় বাষ্প তৈরি করবে, যার ফলে ছিদ্র তৈরি হবে। যদি পরিবেষ্টিত তাপমাত্রা এবং আর্দ্রতা খুব কম হয়, তাহলে সাবস্ট্রেটের পৃষ্ঠে এবং শিল্ডিং গ্যাসে খুব কম আর্দ্রতা থাকবে, জলীয় বাষ্পের উত্পাদন হ্রাস করবে, যার ফলে ছিদ্রগুলি হ্রাস পাবে; গুণমান কর্মীদের ঢালাই স্টেশনে তাপমাত্রা, আর্দ্রতা এবং ধুলোর লক্ষ্য মান সনাক্ত করতে দিন।
চতুর্থত, লেজারের গভীর অনুপ্রবেশ ঢালাইয়ে ছিদ্র কমাতে বা নির্মূল করতে বিম সুইং পদ্ধতি ব্যবহার করা হয়। ঢালাইয়ের সময় সুইং যোগ করার কারণে, ওয়েল্ড সীমে মরীচির আদান-প্রদানের কারণে ওয়েল্ড সীমের অংশ বারবার গলে যায়, যা ওয়েল্ডিং পুলে তরল ধাতুর বসবাসের সময়কে দীর্ঘায়িত করে। একই সময়ে, মরীচির বিচ্যুতিও প্রতি ইউনিট এলাকায় তাপ ইনপুট বাড়ায়। ওয়েল্ডের গভীরতা-থেকে-প্রস্থের অনুপাত হ্রাস পায়, যা বুদবুদের উত্থানের জন্য সহায়ক, যার ফলে ছিদ্রগুলি দূর হয়। অন্যদিকে, রশ্মির সুইং ছোট গর্তকে সেই অনুযায়ী সুইং করে, যা ওয়েল্ডিং পুলের জন্য একটি আলোড়নকারী শক্তিও প্রদান করতে পারে, ওয়েল্ডিং পুলের পরিচলন এবং আলোড়ন বাড়াতে পারে এবং ছিদ্রগুলি নির্মূল করার জন্য একটি উপকারী প্রভাব ফেলে।
পঞ্চম, পালস ফ্রিকোয়েন্সি, পালস ফ্রিকোয়েন্সি প্রতি ইউনিট সময় লেজার রশ্মি দ্বারা নির্গত ডালের সংখ্যা বোঝায়, যা গলিত পুলে তাপ ইনপুট এবং তাপ সঞ্চয়কে প্রভাবিত করবে এবং তারপর গলিত তাপমাত্রার ক্ষেত্র এবং প্রবাহ ক্ষেত্রকে প্রভাবিত করবে। পুল যদি পালস ফ্রিকোয়েন্সি খুব বেশি হয়, তাহলে এটি গলিত পুলে অত্যধিক তাপ প্রবেশের দিকে নিয়ে যাবে, যার ফলে গলিত পুলের তাপমাত্রা খুব বেশি হবে, ধাতব বাষ্প বা অন্যান্য উপাদান তৈরি করবে যা উচ্চ তাপমাত্রায় উদ্বায়ী, ফলে ছিদ্র তৈরি হয়। যদি পালস ফ্রিকোয়েন্সি খুব কম হয়, তবে এটি গলিত পুলে অপর্যাপ্ত তাপ সঞ্চয়ের দিকে পরিচালিত করবে, যার ফলে গলিত পুলের তাপমাত্রা খুব কম হবে, গ্যাসের দ্রবীভূতকরণ এবং অব্যাহতি হ্রাস পাবে, যার ফলে ছিদ্র তৈরি হবে। সাধারণভাবে বলতে গেলে, সাবস্ট্রেট বেধ এবং লেজারের শক্তির উপর ভিত্তি করে একটি যুক্তিসঙ্গত পরিসরের মধ্যে পালস ফ্রিকোয়েন্সি বেছে নেওয়া উচিত এবং খুব বেশি বা খুব কম হওয়া এড়ানো উচিত।
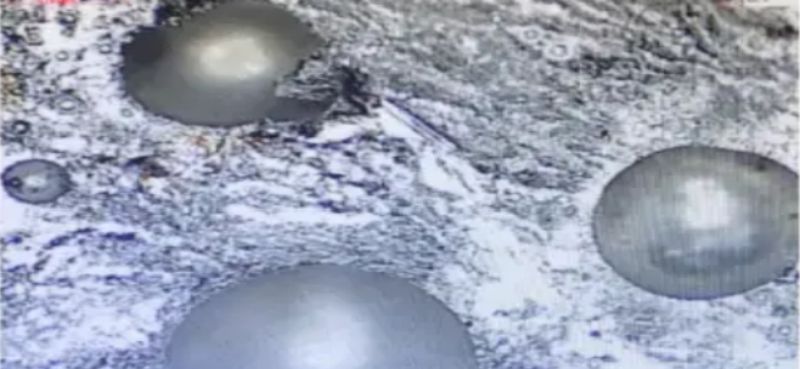
ঢালাই গর্ত (লেজার ঢালাই)
2. ঢালাই স্প্যাটার
ঢালাই প্রক্রিয়া চলাকালীন উত্পন্ন স্প্যাটার, লেজার ঢালাই ওয়েল্ডের পৃষ্ঠের গুণমানকে গুরুতরভাবে প্রভাবিত করবে এবং লেন্সকে দূষিত করবে এবং ক্ষতি করবে। সাধারণ কর্মক্ষমতা নিম্নরূপ: লেজার ঢালাই সম্পন্ন হওয়ার পরে, অনেক ধাতব কণা উপাদান বা ওয়ার্কপিসের পৃষ্ঠে উপস্থিত হয় এবং উপাদান বা ওয়ার্কপিসের পৃষ্ঠে লেগে থাকে। সবচেয়ে স্বজ্ঞাত পারফরম্যান্স হল গ্যালভানোমিটারের মোডে ঢালাই করার সময়, গ্যালভানোমিটারের প্রতিরক্ষামূলক লেন্স ব্যবহার করার পর, পৃষ্ঠে ঘন গর্ত থাকবে এবং এই গর্তগুলি ওয়েল্ডিং স্প্যাটার দ্বারা সৃষ্ট হয়। দীর্ঘ সময়ের পরে, আলোটি ব্লক করা সহজ, এবং ঢালাই আলোতে সমস্যা হবে, ফলে ভাঙা ঢালাই এবং ভার্চুয়াল ঢালাইয়ের মতো সমস্যাগুলির একটি সিরিজ হবে।
স্প্ল্যাশিং এর কারণ কি?
প্রথমত, শক্তির ঘনত্ব, শক্তির ঘনত্ব যত বেশি হবে, স্প্যাটার তৈরি করা তত সহজ হবে এবং স্প্যাটার সরাসরি পাওয়ার ঘনত্বের সাথে সম্পর্কিত। এটি একটি শতাব্দী প্রাচীন সমস্যা। অন্তত এখন পর্যন্ত, শিল্প স্প্ল্যাশিং সমস্যা সমাধান করতে পারেনি, এবং শুধুমাত্র এটি সামান্য হ্রাস করা হয়েছে বলতে পারেন. লিথিয়াম ব্যাটারি শিল্পে, স্প্ল্যাশিং ব্যাটারি শর্ট সার্কিটের সবচেয়ে বড় অপরাধী, কিন্তু এটি মূল কারণ সমাধান করতে সক্ষম হয়নি। ব্যাটারিতে স্প্যাটারের প্রভাব শুধুমাত্র সুরক্ষার দৃষ্টিকোণ থেকে হ্রাস করা যেতে পারে। উদাহরণস্বরূপ, ঢালাইয়ের অংশের চারপাশে ধুলো অপসারণ পোর্টের একটি বৃত্ত এবং প্রতিরক্ষামূলক কভার যুক্ত করা হয় এবং স্প্যাটারের প্রভাব বা এমনকি ব্যাটারির ক্ষতি রোধ করার জন্য বৃত্তে বায়ু ছুরির সারি যুক্ত করা হয়। ওয়েল্ডিং স্টেশনের আশেপাশের পরিবেশ, পণ্য এবং উপাদানগুলি ধ্বংস করার উপায়গুলি শেষ হয়ে গেছে বলা যেতে পারে।
স্প্যাটার সমস্যা সমাধানের জন্য, এটি কেবল বলা যেতে পারে যে ঢালাই শক্তি হ্রাস স্প্যাটার কমাতে সাহায্য করে। অনুপ্রবেশ অপর্যাপ্ত হলে ঢালাইয়ের গতি হ্রাস করাও সাহায্য করতে পারে। কিন্তু কিছু বিশেষ প্রক্রিয়ার প্রয়োজনে, এর প্রভাব কম। এটি একই প্রক্রিয়া, বিভিন্ন মেশিন এবং বিভিন্ন ব্যাচের উপকরণগুলির সম্পূর্ণ ভিন্ন ঢালাই প্রভাব রয়েছে। অতএব, নতুন শক্তি শিল্পে একটি অলিখিত নিয়ম রয়েছে, এক টুকরো সরঞ্জামের জন্য ঢালাইয়ের পরামিতিগুলির একটি সেট।
দ্বিতীয়ত, যদি প্রক্রিয়াকৃত উপাদান বা ওয়ার্কপিসের পৃষ্ঠ পরিষ্কার না করা হয়, তাহলে তেলের দাগ বা দূষকগুলিও মারাত্মক স্প্ল্যাশ সৃষ্টি করবে। এই সময়ে, সবচেয়ে সহজ জিনিস প্রক্রিয়াজাত উপাদান পৃষ্ঠ পরিষ্কার করা হয়।
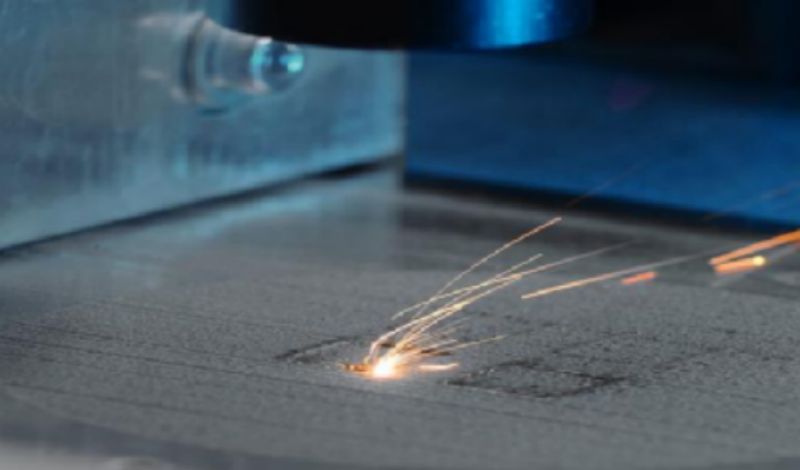
3. লেজার ঢালাই উচ্চ প্রতিফলনশীলতা
সাধারণভাবে বলতে গেলে, উচ্চ প্রতিফলন বলতে বোঝায় যে প্রক্রিয়াকরণ উপাদানটির একটি ছোট প্রতিরোধ ক্ষমতা, তুলনামূলকভাবে মসৃণ পৃষ্ঠ এবং কাছাকাছি-ইনফ্রারেড লেজারগুলির জন্য একটি কম শোষণ হার, যা প্রচুর পরিমাণে লেজার নির্গমনের দিকে পরিচালিত করে, এবং কারণ বেশিরভাগ লেজার ব্যবহার করা হয়। উল্লম্বভাবে উপাদান বা স্বল্প পরিমাণে প্রবণতার কারণে, ফিরে আসা লেজারের আলো আউটপুট মাথায় পুনরায় প্রবেশ করে এবং এমনকি ফিরে আসা আলোর কিছু অংশ শক্তি-প্রেরণকারী ফাইবারে মিলিত হয় এবং ফাইবার বরাবর ভিতরের দিকে প্রেরণ করা হয়। লেজারের, লেজারের ভিতরের মূল উপাদানগুলি উচ্চ তাপমাত্রায় চলতে থাকে।
লেজার ঢালাইয়ের সময় প্রতিফলন খুব বেশি হলে, নিম্নলিখিত সমাধানগুলি নেওয়া যেতে পারে:
3.1 অ্যান্টি-প্রতিফলন আবরণ ব্যবহার করুন বা উপাদানের পৃষ্ঠের চিকিত্সা করুন: একটি অ্যান্টি-রিফ্লেকশন লেপ দিয়ে ঢালাই উপাদানের পৃষ্ঠকে লেজার কার্যকরভাবে লেজারের প্রতিফলন হ্রাস করতে পারে। এই আবরণটি সাধারণত কম প্রতিফলন সহ একটি বিশেষ অপটিক্যাল উপাদান যা লেজার শক্তি শোষণ করে এটিকে প্রতিফলিত করার পরিবর্তে। কিছু প্রক্রিয়ায়, যেমন বর্তমান সংগ্রাহক ঢালাই, নরম সংযোগ ইত্যাদি, পৃষ্ঠটি এমবসড করা যেতে পারে।
3.2 ঢালাই কোণ সামঞ্জস্য করুন: ঢালাই কোণ সামঞ্জস্য করে, লেজার রশ্মি আরও উপযুক্ত কোণে ঢালাই উপাদানের উপর ঘটনা হতে পারে এবং প্রতিফলনের ঘটনা কমাতে পারে। সাধারণত, ঢালাই করার জন্য উপাদানটির পৃষ্ঠের সাথে লেজার রশ্মির ঘটনাটি লম্বভাবে থাকা প্রতিফলন হ্রাস করার একটি ভাল উপায়।
3.3 সহায়ক শোষক যোগ করা: ঢালাই প্রক্রিয়া চলাকালীন, একটি নির্দিষ্ট পরিমাণ সহায়ক শোষক, যেমন পাউডার বা তরল, জোড়ের সাথে যোগ করা হয়। এই শোষকগুলি লেজারের শক্তি শোষণ করে এবং প্রতিফলন হ্রাস করে। নির্দিষ্ট ঢালাই উপকরণ এবং প্রয়োগের পরিস্থিতির উপর ভিত্তি করে উপযুক্ত শোষক নির্বাচন করা প্রয়োজন। লিথিয়াম ব্যাটারি শিল্পে, এটি অসম্ভাব্য।
3.4 লেজার প্রেরণ করতে অপটিক্যাল ফাইবার ব্যবহার করুন: যদি সম্ভব হয়, অপটিক্যাল ফাইবার ব্যবহার করা যেতে পারে লেজারকে ঢালাই অবস্থানে প্রেরণ করতে যাতে প্রতিফলন কম হয়। অপটিক্যাল ফাইবার ঢালাইয়ের উপাদানের পৃষ্ঠের সরাসরি এক্সপোজার এড়াতে এবং প্রতিফলনের ঘটনা কমাতে লেজারের রশ্মিকে ঢালাই এলাকায় গাইড করতে পারে।
3.5 লেজারের পরামিতি সামঞ্জস্য করা: লেজারের শক্তি, ফোকাল দৈর্ঘ্য এবং ফোকাল ব্যাসের মতো পরামিতিগুলি সামঞ্জস্য করে, লেজার শক্তির বন্টন নিয়ন্ত্রণ করা যায় এবং প্রতিফলন হ্রাস করা যায়। কিছু প্রতিফলিত উপকরণের জন্য, লেজার শক্তি হ্রাস প্রতিফলন কমাতে একটি কার্যকর উপায় হতে পারে।
3.6 একটি বিম স্প্লিটার ব্যবহার করুন: একটি বিম স্প্লিটার লেজারের শক্তির অংশকে শোষণ ডিভাইসে নিয়ে যেতে পারে, যার ফলে প্রতিফলনের ঘটনা হ্রাস পায়। রশ্মি বিভাজন ডিভাইসে সাধারণত অপটিক্যাল উপাদান এবং শোষক থাকে এবং উপযুক্ত উপাদান নির্বাচন করে এবং ডিভাইসের বিন্যাস সামঞ্জস্য করে, নিম্ন প্রতিফলিততা অর্জন করা যায়।
4. ঢালাই আন্ডারকাট
লিথিয়াম ব্যাটারি উত্পাদন প্রক্রিয়ায়, কোন প্রক্রিয়াগুলি আন্ডারকাটিং হওয়ার সম্ভাবনা বেশি? আন্ডারকাটিং কেন ঘটে? এর বিশ্লেষণ করা যাক.
আন্ডারকাট, সাধারণত ঢালাইয়ের কাঁচামালগুলি একে অপরের সাথে ভালভাবে মিলিত হয় না, ব্যবধানটি খুব বড় বা খাঁজ দেখা যায়, গভীরতা এবং প্রস্থ মূলত 0.5 মিমি-এর বেশি, মোট দৈর্ঘ্য ওয়েল্ড দৈর্ঘ্যের 10% এর বেশি, বা পণ্য প্রক্রিয়া মান অনুরোধকৃত দৈর্ঘ্যের চেয়ে বেশি।
পুরো লিথিয়াম ব্যাটারি উত্পাদন প্রক্রিয়ায়, আন্ডারকাটিং হওয়ার সম্ভাবনা বেশি, এবং এটি সাধারণত সিলিং প্রি-ওয়েল্ডিং এবং নলাকার কভার প্লেটের ঢালাই এবং বর্গাকার অ্যালুমিনিয়াম শেল কভার প্লেটের সিলিং প্রাক-ঢালাই এবং ঢালাইয়ে বিতরণ করা হয়। প্রধান কারণ হল যে সিলিং কভার প্লেটকে শেলের সাথে ঢালাইয়ের জন্য সহযোগিতা করতে হবে, সিলিং কভার প্লেট এবং শেলের মধ্যে ম্যাচিং প্রক্রিয়াটি অত্যধিক ঢালাই ফাঁক, খাঁজ, ধসে পড়া ইত্যাদির প্রবণতা রয়েছে, তাই এটি বিশেষত আন্ডারকাট হওয়ার ঝুঁকিপূর্ণ। .
তাই আন্ডারকাটিং কারণ কি?
যদি ঢালাইয়ের গতি খুব দ্রুত হয়, তাহলে ওয়েল্ডের কেন্দ্রের দিকে নির্দেশ করে ছোট গর্তের পিছনের তরল ধাতুটি পুনরায় বিতরণ করার সময় পাবে না, যার ফলে ওয়েল্ডের উভয় পাশে দৃঢ়তা এবং আন্ডারকাটিং হবে। উপরের পরিস্থিতির পরিপ্রেক্ষিতে, আমাদের ঢালাইয়ের পরামিতিগুলি অপ্টিমাইজ করতে হবে। এটাকে সহজভাবে বলতে গেলে, বিভিন্ন পরামিতি যাচাই করার জন্য বারবার পরীক্ষা করা হয় এবং উপযুক্ত পরামিতি পাওয়া না যাওয়া পর্যন্ত DOE করতে থাকে।
2. ঢালাইয়ের উপকরণের অত্যধিক ঢালাই ফাঁক, খাঁজ, ধসে পড়া, ইত্যাদি গলিত ধাতুর শূন্যস্থান পূরণ করার পরিমাণ কমিয়ে দেবে, যার ফলে আন্ডারকাট হওয়ার সম্ভাবনা বেশি হবে। এটি সরঞ্জাম এবং কাঁচামালের প্রশ্ন। ঢালাইয়ের কাঁচামালগুলি আমাদের প্রক্রিয়ার আগত উপাদানের প্রয়োজনীয়তাগুলি পূরণ করে কিনা, সরঞ্জামগুলির যথার্থতা প্রয়োজনীয়তাগুলি পূরণ করে কিনা, ইত্যাদি৷ স্বাভাবিক অভ্যাস হল ক্রমাগতভাবে সরবরাহকারী এবং সরঞ্জামের দায়িত্বে থাকা ব্যক্তিদের নির্যাতন এবং মারধর করা৷
3. লেজার ঢালাইয়ের শেষে শক্তি খুব দ্রুত কমে গেলে, ছোট গর্তটি ভেঙে যেতে পারে, যার ফলে স্থানীয় আন্ডারকাটিং হয়। শক্তি এবং গতির সঠিক মিল কার্যকরভাবে আন্ডারকাট গঠন প্রতিরোধ করতে পারে। পুরানো কথাটি বলে, পরীক্ষাগুলি পুনরাবৃত্তি করুন, বিভিন্ন পরামিতি যাচাই করুন এবং আপনি সঠিক প্যারামিটারগুলি না পাওয়া পর্যন্ত DOE চালিয়ে যান।
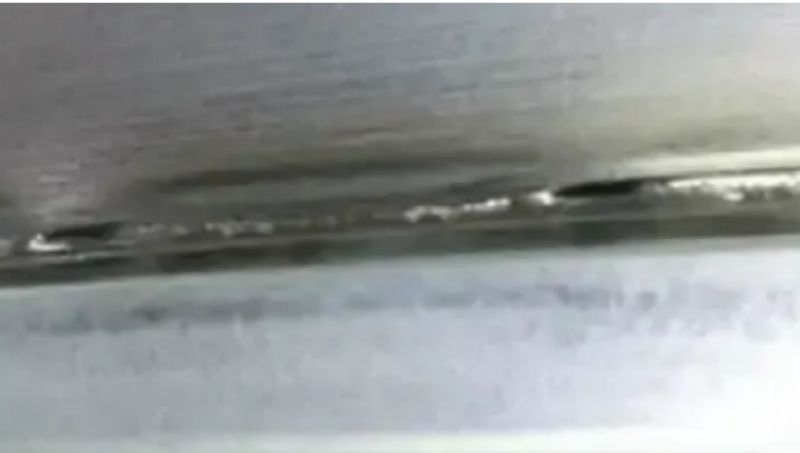
5. ঢালাই কেন্দ্র পতন
ঢালাইয়ের গতি ধীর হলে, গলিত পুলটি বড় এবং প্রশস্ত হবে, গলিত ধাতুর পরিমাণ বৃদ্ধি পাবে। এটি পৃষ্ঠের টান বজায় রাখা কঠিন করে তুলতে পারে। যখন গলিত ধাতু খুব ভারী হয়ে যায়, তখন জোড়ের কেন্দ্রটি ডুবে যেতে পারে এবং ডিপ এবং গর্ত তৈরি করতে পারে। এই ক্ষেত্রে, গলিত পুলের পতন রোধ করার জন্য শক্তির ঘনত্ব যথাযথভাবে হ্রাস করা দরকার।
অন্য পরিস্থিতিতে, ঢালাই ফাঁক ছিদ্র সৃষ্টি না করে শুধু একটি পতন গঠন করে। এটি নিঃসন্দেহে সরঞ্জাম প্রেস ফিট একটি সমস্যা.
লেজার ঢালাইয়ের সময় যে ত্রুটিগুলি ঘটতে পারে এবং বিভিন্ন ত্রুটির কারণগুলির একটি সঠিক বোধগম্যতা যেকোনো অস্বাভাবিক ঢালাই সমস্যা সমাধানের জন্য আরও লক্ষ্যযুক্ত পদ্ধতির জন্য অনুমতি দেয়।
6. জোড় ফাটল
ক্রমাগত লেজার ঢালাইয়ের সময় যে ফাটলগুলি দেখা যায় তা মূলত তাপীয় ফাটল, যেমন স্ফটিক ফাটল এবং লিকুইফেকশন ফাটল। এই ফাটলগুলির প্রধান কারণ হল ঢালাই সম্পূর্ণরূপে দৃঢ় হওয়ার আগে উত্পন্ন বৃহৎ সংকোচন শক্তি।
এছাড়াও লেজার ওয়েল্ডিংয়ে ফাটলের জন্য নিম্নলিখিত কারণ রয়েছে:
1. অযৌক্তিক ওয়েল্ড ডিজাইন: ওয়েল্ডের জ্যামিতি এবং আকারের অনুপযুক্ত নকশা ওয়েল্ডিং স্ট্রেস ঘনত্বের কারণ হতে পারে, যার ফলে ফাটল সৃষ্টি হতে পারে। সমাধান ঢালাই চাপ ঘনত্ব এড়াতে ঝালাই নকশা অপ্টিমাইজ করা হয়. আপনি উপযুক্ত অফসেট ঢালাই ব্যবহার করতে পারেন, ঢালাই আকৃতি পরিবর্তন করতে পারেন, ইত্যাদি।
2. ঢালাইয়ের পরামিতিগুলির অমিল: ঢালাইয়ের পরামিতিগুলির অনুপযুক্ত নির্বাচন, যেমন খুব দ্রুত ঢালাইয়ের গতি, খুব বেশি শক্তি, ইত্যাদি, ঢালাই এলাকায় অসম তাপমাত্রার পরিবর্তন হতে পারে, যার ফলে বড় ঢালাই চাপ এবং ফাটল দেখা দিতে পারে। সমাধান হল নির্দিষ্ট উপাদান এবং ঢালাই অবস্থার সাথে মেলে ঢালাই পরামিতি সামঞ্জস্য করা।
3. ঢালাই পৃষ্ঠের দুর্বল প্রস্তুতি: ঢালাইয়ের আগে ঢালাইয়ের পৃষ্ঠকে সঠিকভাবে পরিষ্কার এবং প্রাক-চিকিত্সা করতে ব্যর্থতা, যেমন অক্সাইড, গ্রীস ইত্যাদি অপসারণ, ঢালাইয়ের গুণমান এবং শক্তিকে প্রভাবিত করবে এবং সহজেই ফাটল সৃষ্টি করবে। সমাধান হল ঢালাইয়ের অংশে থাকা অমেধ্য এবং দূষকগুলি কার্যকরভাবে চিকিত্সা করা নিশ্চিত করার জন্য ঢালাই পৃষ্ঠকে পর্যাপ্তভাবে পরিষ্কার করা এবং পূর্ব-চিকিত্সা করা।
4. ঢালাই তাপ ইনপুটের অনুপযুক্ত নিয়ন্ত্রণ: ঢালাইয়ের সময় তাপ ইনপুটের দুর্বল নিয়ন্ত্রণ, যেমন ঢালাইয়ের সময় অত্যধিক তাপমাত্রা, ঢালাই স্তরের অনুপযুক্ত শীতল হার ইত্যাদি, ঢালাই এলাকার গঠনে পরিবর্তন আনবে, ফলে ফাটল দেখা দেবে। . সমাধান হল অতিরিক্ত গরম এবং দ্রুত শীতল হওয়া এড়াতে ঢালাইয়ের সময় তাপমাত্রা এবং শীতল করার হার নিয়ন্ত্রণ করা।
5. অপর্যাপ্ত স্ট্রেস রিলিফ: ঢালাইয়ের পরে অপর্যাপ্ত স্ট্রেস রিলিফ ট্রিটমেন্টের ফলে ঢালাই করা জায়গায় অপর্যাপ্ত স্ট্রেস রিলিফ হবে, যা সহজেই ফাটল সৃষ্টি করবে। সমাধান হল ঢালাইয়ের পরে উপযুক্ত স্ট্রেস রিলিফ ট্রিটমেন্ট করা, যেমন হিট ট্রিটমেন্ট বা ভাইব্রেশন ট্রিটমেন্ট (প্রধান কারণ)।
লিথিয়াম ব্যাটারির উত্পাদন প্রক্রিয়ার জন্য, কোন প্রক্রিয়াগুলি ফাটল সৃষ্টি করার সম্ভাবনা বেশি?
সাধারণত, সিলিং ঢালাইয়ের সময় ফাটল হওয়ার সম্ভাবনা থাকে, যেমন নলাকার স্টিলের খোসা বা অ্যালুমিনিয়াম শেলগুলির সিলিং ঢালাই, বর্গাকার অ্যালুমিনিয়াম শেলগুলির সিলিং ঢালাই ইত্যাদি। উপরন্তু, মডিউল প্যাকেজিং প্রক্রিয়া চলাকালীন, বর্তমান সংগ্রাহকের ঢালাইও প্রবণ। ফাটল থেকে
অবশ্যই, আমরা এই ফাটলগুলি কমাতে বা দূর করতে ফিলার ওয়্যার, প্রিহিটিং বা অন্যান্য পদ্ধতিও ব্যবহার করতে পারি।
পোস্টের সময়: সেপ্টেম্বর-০১-২০২৩